What is FactorySight?
Provides real-time insights by rapidly collecting, storing, and visualizing manufacturing equipment data.
Real-Time Collection of Large-Scale Equipment Data
-
Stable collection of over 35,000 tags per second
(Daily: 3 billion records / Monthly: 90 billion records)
Insight through Visualization of Equipment Data
-
Real-time production equipment monitoring (design), graphs, and charts
PLC and Standard Protocol Support
-
Provides standard PLC drivers and standard protocols
Solution Feature Overview
Collects and stores data from on-site equipment such as PLCs, and utilizes it comprehensively through visualization, analysis, and monitoring features
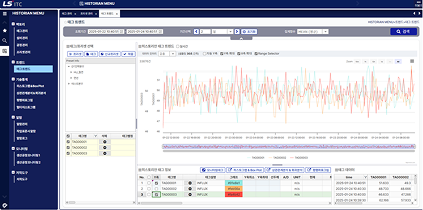
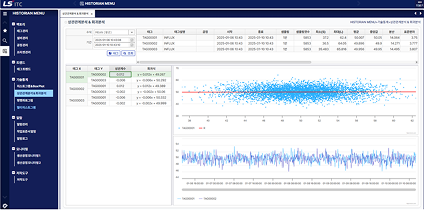
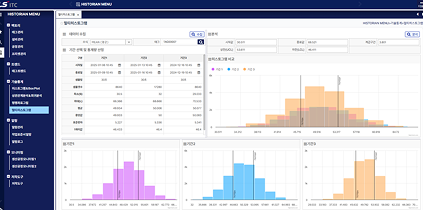
Data Collection
- Device Registration and Identification
- Device Metadata
- Device Data Collection
- Tag Definition and Management
- User-Defined Tag Set
- Data Storage
- Data Collection Cycle Management
Data Preprocessing
- Data Filtering
- Data Aggregation
- Missing Value
Data Visualization
- Correlation Analysis
- Regression Analysis
- Histogram
- Tag Data Trend
- Real-time Tag Data Trend
- Design Studio
Alarm
- Tag alarm
- SOP(Standard Operating Procedure) Alarm
- Alarm History