Key Features
Enhances responsiveness to supply chain variability in manufacturing, optimizes inventory levels, and improves production efficiency. It establishes optimized production plans based on on-time delivery and production efficiency, as well as issued orders and available lots.
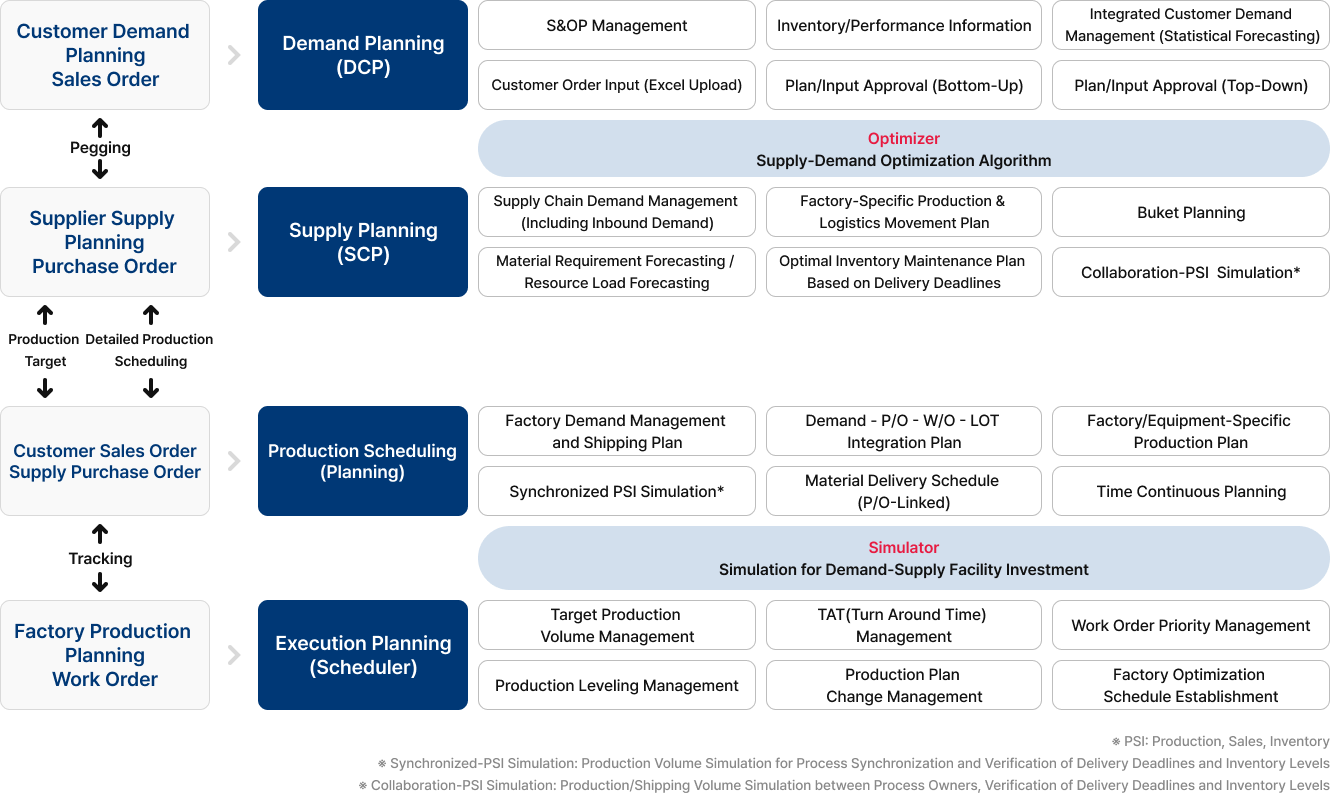