Key Features
Provides standardized production management processes based on MESA and ISA-95, along with comprehensive control over core manufacturing areas such as process management, quality assurance, material tracking, and KPI monitoring.
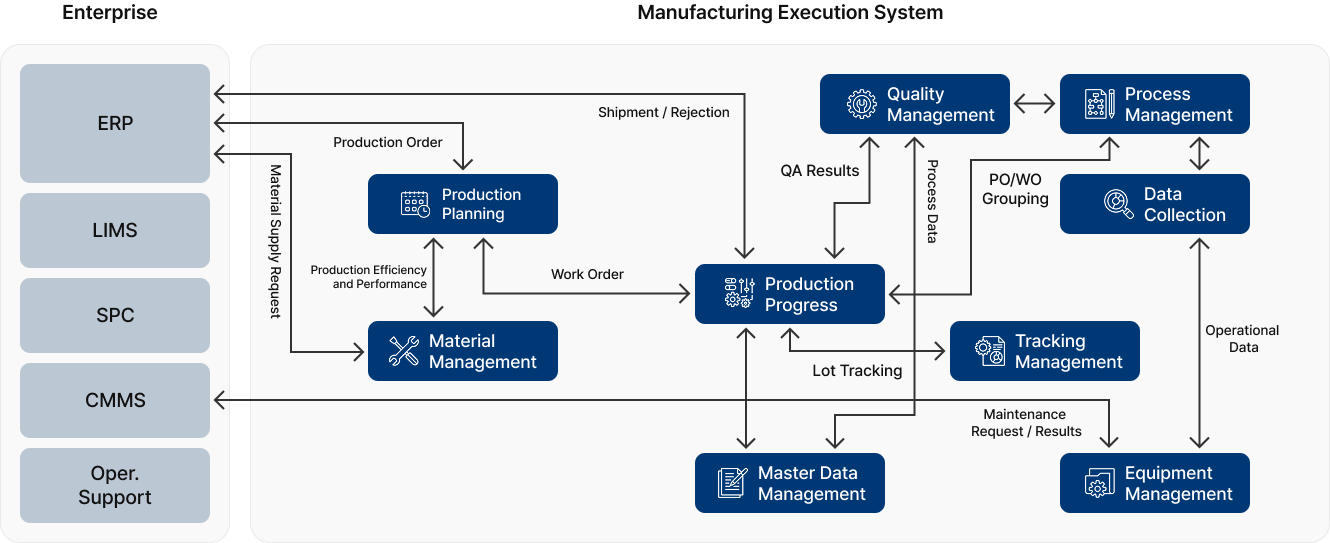
Advanced Functions (High-Tech)
- Process/Inspection/Shipment Lot + Process Data Mapping
- Production/Inspection Equipment Control and Alarm Information Interface
- Auto Lot Tracking & Traceability
- Work Order-Based Raw and Sub-material Mixing Ratio Management
- Import, Process, and Shipment Inspection Recovery Rate/Yield Management
- Manufacturing/Quality Anomaly and Change Management
Basic Functions
Production Planning
-
Purchase/Work Order Management
-
Input Management (Loading/Unloading)
Process Management / Quality Management
-
Work Status Management (Start/End)
-
Hold/Release/Rework Management
-
Process Inspection (CTQ/CTP) Management
Material Management / Shipment Management
-
Consumable Material Management
-
WIP Continuity and Handling Material Management
Equipment Management / KPI
-
Equipment Status, Operation Management
-
KPI Management (Real -Time Monitoring)