Key Features
Manages transport instructions, route optimization, and dispatching rules in coordination with various logistics transport equipment
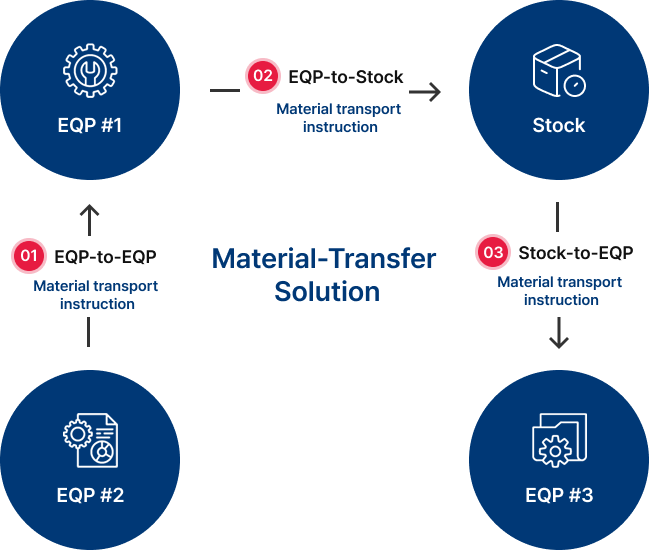
Equipment Interface (AMHS*)
- Storage :
Stocker*, Load Port/ Buffer Station
- Transfer Machine :
OHT*, AGV, ...
Material transport instruction management
-
Instruction error handling and exception management
-
Queue processing and optimization (priority list, resource allocation, etc.)
Transport route optimization
-
Carrier location management (location tracking, etc.)
-
Carrier specifications and status management (size, staging location, etc.)
-
Route classification and optimization (destination type, priority, etc.)
- * AMHS (Automated Material Handling System Equipment): Equipment for automated material transport
- * OHT (Overhead Hoist Transport): Transport system that moves along overhead rails
- * Stocker: Automated storage system for temporarily holding materials
- * Load Port / Buffer: Interface device for material transfer between equipment and AMHS
Flexible IT Architecture
-
Open architecture for system integration (DB-independent)
-
Modern IT platform based on Java
-
Integrated development employment and deployment function for customization
Industry-Specific Modular Functions
-
Modularization of MCS functions based on SEMI/SEMATECH standards for the semiconductor industry
-
Modularized support for specialized equipment based on experience in semiconductor, FPD, and secondary battery packaging industries
-
Independent functional module structure
Scalability-Oriented Design
-
Supports various communication protocols such as Web Service, TCP/IP, and TIB/RV
-
Supports database scalability (userdefined columns, tables, etc.)
-
Supports rule-based business logic extensibility