Key Features
Determines lot and equipment priorities and issues transport instructions by configuring dispatching rules and linking with the Material Control System (MCS).
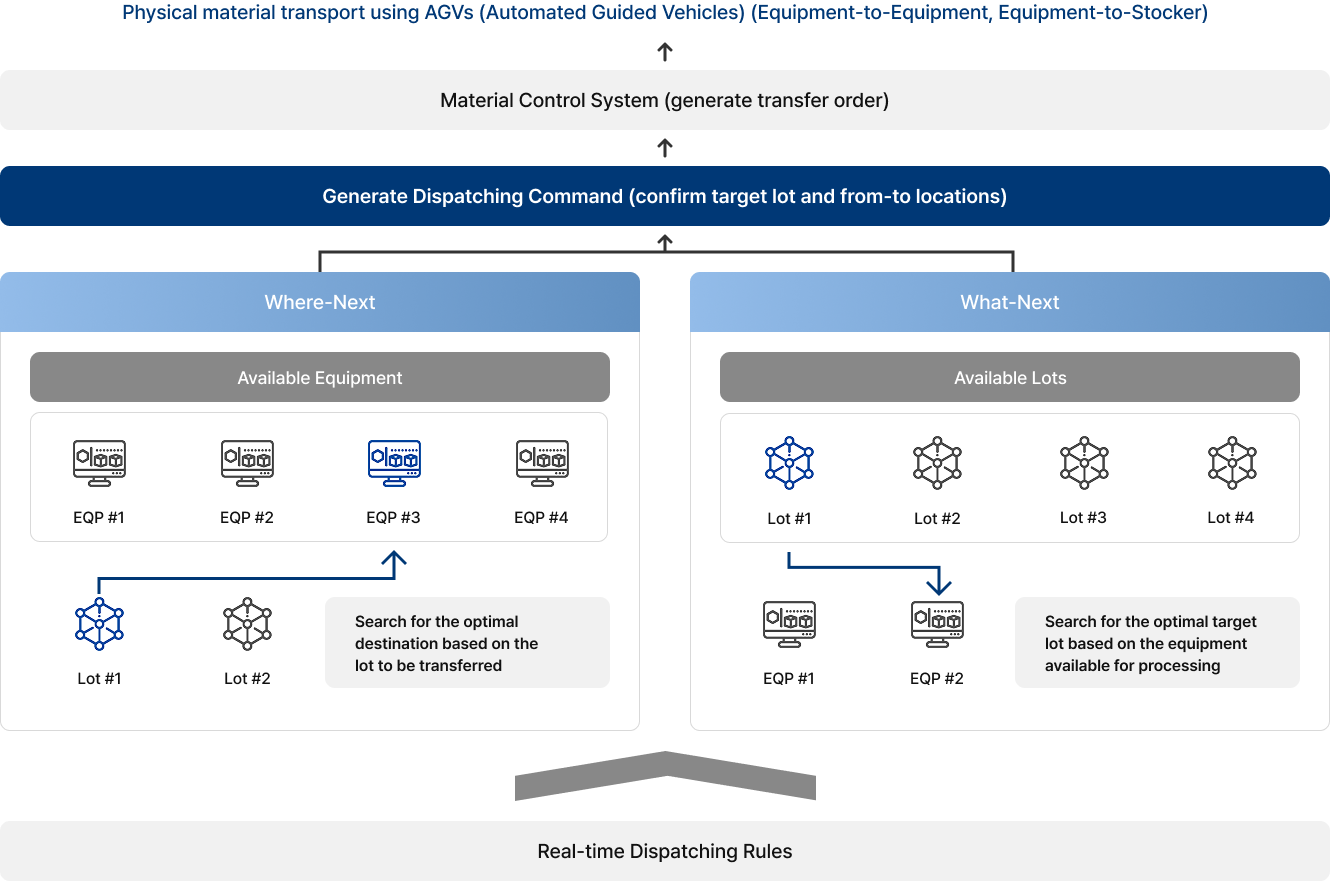
Dispatching Rule
-
What-Next rule (lot selection rule)
-
Where-Next rule (equipment selection rule)
-
Rule simulation function
Defect Analysis / Rule Improvement Management
-
Create priority rules based on various conditions - Same product/spec/production order priority rule - Priority-based rule - Reserved product priority rule - Queue time-based priority rule - Due date-based priority rule - Equipment with max idle port priority rule
Quality Certification / Document Management
-
View rule information applied to each process and equipment
-
Rule copy & phase function
-
Change history management of rules by process/equipment
-
Report on dispatched lots by process and equipment