Key Features
An equipment control software development tool that provides integrated support from equipment data modeling to communication interface and control logic development.
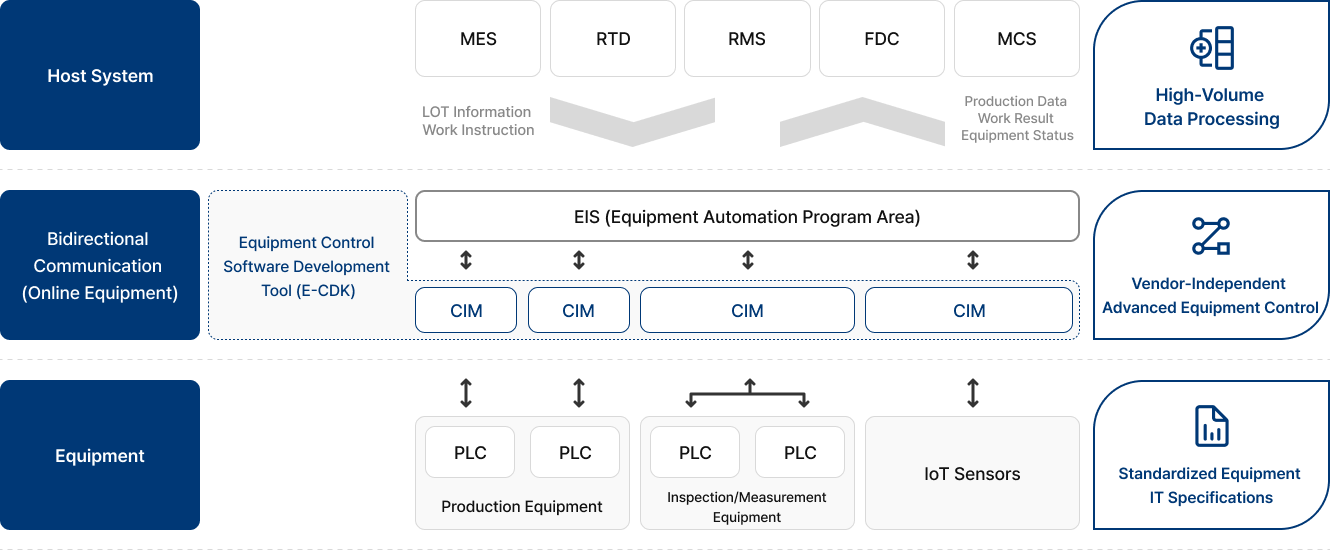
Integrated Modeling Tool
-
Equipment configuration setup
-
External I/O data configuration
-
Workflow editing and configuration
External Communication Interface
-
Scalable plug -in architecture
-
Separate industrial standard communication drivers provided (OPC, PLC, Modbus, etc.)
-
Easy access based on data name
Workflow & Libraries
-
Workflow for user logic development
-
Various additional activities provided
-
WorkerQueue library provided
-
Functions for data processing provided
-
Log handling functions provided