Goals
Bridging Physical and Digital — converting Physical to Digital and Digital to Physical, and validating manufacturing site changes in the virtual space.
- Manual Data
- Automatic Data
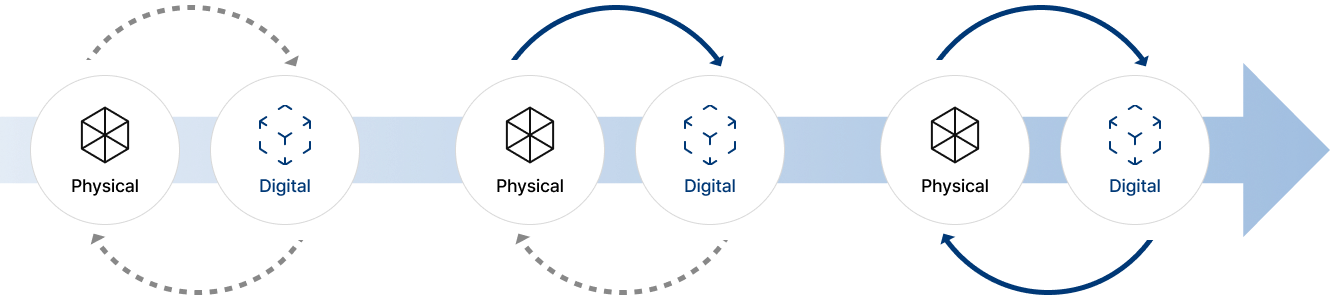
New Factory and Line Construction Plan Review
-
Pre-assess physical and systematic limitations and make adjustments
-
Identify issues in advance and apply improvement measures
Visual and Quantitative Analysis of Existing Manufacturing Site Pain Points
-
Identify problems for each line through existing line simulation
-
Review production volumes and material flow when expanding the factory
Justification of Manufacturing Site Improvement
-
Simulation and reporting based on equipment and process data
-
Enhanced persuasiveness with 3D simulation elements